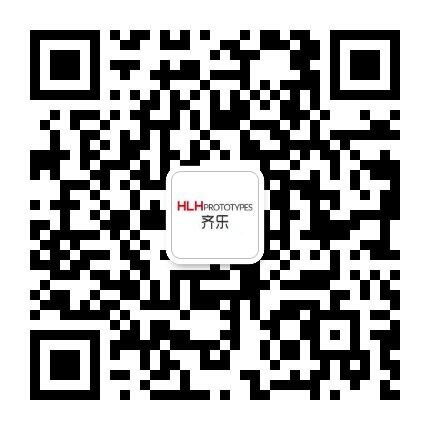
微信客服

在線客服
汽車鈑金手板
發布時間:2025年06月27日
汽車鈑金手板是汽車外觀件(如車門、引擎蓋、尾箱、翼子板等)的原型件,用于驗證設計、裝配和工藝可行性。以下是針對汽車鈑金手板的詳細制作流程和技術要點:
明確需求
用途:驗證外觀造型、裝配匹配性、結構強度、焊接工藝或涂裝效果。
材料:根據零件位置選擇材料,如冷軋鋼板(普通車身)、鋁合金(輕量化部件)、不銹鋼(防銹部件)或碳纖維(高性能部件)。
數量:小批量(1~5件)通常采用數控加工或快速成型,中批量(5~20件)可考慮簡易模具沖壓。
設計關鍵點
曲面精度:汽車鈑金多為復雜曲面,需確?;《?、輪廓與設計一致(公差±0.2mm)。
拔模斜度:針對沖壓工藝,設置合理的拔模斜度(通常3°~5°),避免脫模困難。
裝配孔/定位孔:精準標注裝配孔、焊接點或卡扣位置,確保與周邊零件匹配。
適用場景:小批量、高精度或復雜曲面零件(如概念車鈑金件)。
材料:
鋁合金(6061/6063):輕質且易加工,適合功能性驗證。
鋼材(SPCC/SECC):普通冷軋鋼板,適合仿真量產工藝。
工藝特點:
使用五軸聯動機床加工復雜曲面,精度可達±0.1mm。
表面需拋光或噴砂處理,模擬量產電鍍或涂裝效果。
適用場景:中批量、需要仿真沖壓工藝的鈑金件。
流程:
開發簡易沖壓模具(鋅合金?;驑渲#?,周期短(約7~15天)。
材料可選冷軋鋼板(SPCC)或鍍鋅板(SECC),厚度1.0mm~2.0mm。
優勢:模擬量產沖壓效果,成本低,適合驗證成形性、拉深比和回彈問題。
適用場景:緊急驗證外觀或結構,無需高精度裝配。
材料:
光敏樹脂(SLA/DLP):適合復雜曲面和細節(如格柵、Logo)。
尼龍(SLS):適合功能性零件(如鉸鏈、支架)。
后處理:打磨、噴漆或電鍍,提升外觀質感。
打磨與焊接
數控加工件:用砂紙(從80目到1200目)逐級打磨,去除刀痕。
沖壓件:對拉深痕跡或毛刺進行拋光,必要時激光補焊。
表面處理
電鍍/噴涂:
電鍍鉻/鎳:模擬量產鍍層效果,提升耐腐蝕性和光澤度。
噴烤漆:根據設計要求噴涂金屬漆或啞光漆(如PPG、阿克蘇涂料)。
紋理處理:通過皮紋壓印或激光蝕刻模擬量產紋理(如啞光顆粒感)。
裝配與測試
組裝鈑金件與相鄰零件(如車門與車框、引擎蓋與鎖扣),測試裝配間隙(通常≤0.5mm)。
驗證功能性:
開閉耐久性:測試車門/引擎蓋的開合次數(如10萬次無變形)。
抗震性:模擬顛簸路況,檢查鈑金件是否松動或異響。
防水性:對車門、尾箱等密封部位進行淋雨測試(IPX5等級)。
尺寸檢測
使用三坐標測量儀或激光掃描儀檢測關鍵尺寸(如長寬、弧度、孔位),對比CAD模型。
確保裝配間隙均勻(如車門與車身間隙≤0.5mm)。
外觀檢查
檢查表面是否有劃痕、凹坑、橘皮紋(噴涂缺陷)或沖壓拉裂(材料回彈問題)。
確認顏色一致性(使用色差儀ΔE≤1.5)。
結構優化
根據測試反饋調整設計:
加強筋布局:在薄弱區域增加筋條,提升剛度。
拔模斜度調整:優化模具角度,減少脫模阻力。
材料厚度優化:根據受力分析調整板材厚度(如1.0mm→1.2mm)。
材料回彈控制
鋁合金/鋼材沖壓后易回彈,需通過模具補償或熱處理(如時效硬化)減少變形。
焊接工藝仿真
若鈑金件需焊接(如車門鉸鏈),需驗證焊點位置、強度及熱影響區(HAZ)變形。
成本與周期平衡
CNC加工適合高精度單件,沖壓軟模適合中批量,鋼模開發周期長但適合大批量。
環保與安全
涂裝材料需符合汽車行業環保標準(如VOC排放限制)。
尖銳邊角需倒角處理,避免劃傷風險。
通過以上流程,可高效制作出符合汽車行業標準的鈑金手板,幫助客戶快速驗證設計、優化工藝,并為量產提供可靠數據支持。
上一篇: 機殼類手板加工注意事項
下一篇: 沖壓件手板加工注意事項