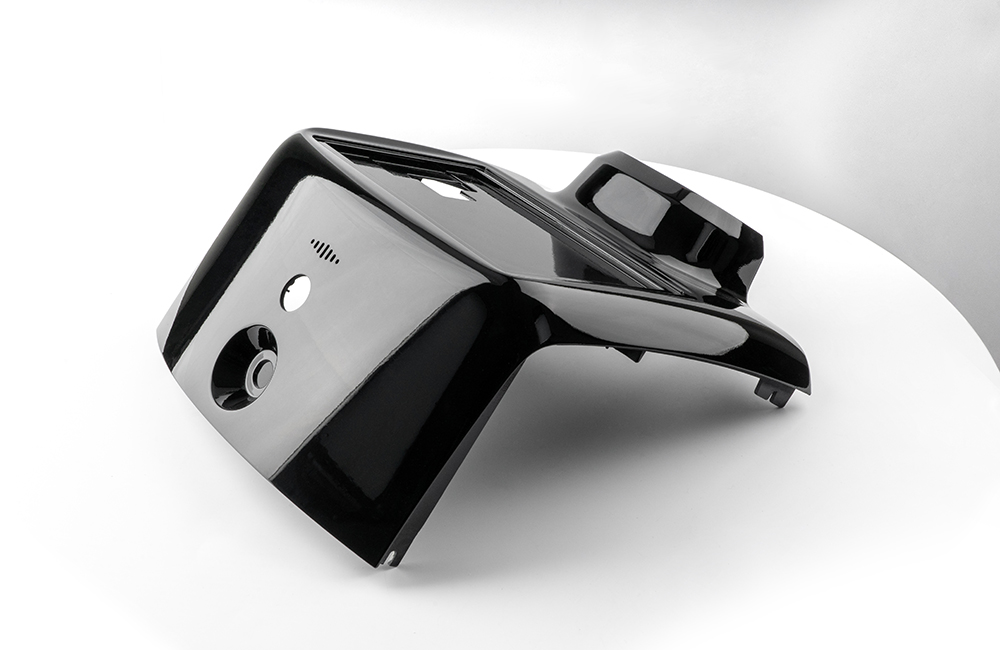
行業/分類:其他手板模型加工
加工方式: cnc加工 使用材料: 塑料
最小精度: 0.05mm 生產周期: 2~7天
產品尺寸: 18cm*15cm*12cm
后處理: 噴油
以下是關于CNC加工汽車零件外殼模型的詳細內容:
一、前期準備
設計模型:使用專業的三維建模軟件,如UG、Pro/E或SolidWorks等,根據汽車零件外殼的功能、形狀和尺寸要求進行精確設計。在設計過程中,需充分考慮外殼的結構強度、裝配關系以及外觀美學等因素,確保模型的準確性和可行性。
材料選擇:常見的汽車零件外殼材料有鋁合金、鋼材、復合材料等。鋁合金具有重量輕、強度高、耐腐蝕等優點,適用于一些對重量要求較高的零部件;鋼材則具有較高的強度和硬度,常用于承受較大載荷的部位;復合材料可根據具體需求定制性能,如碳纖維復合材料具有高強度、低密度的特性,但成本相對較高。選擇時需綜合考慮零件的使用要求、成本、加工工藝等因素。
刀具與切削參數確定:根據加工材料和零件的形狀、尺寸,選擇合適的刀具。例如,對于鋁合金零件,可選用硬質合金刀具;對于鋼材,可能需要使用更耐磨的涂層刀具。同時,確定合理的切削參數,包括切削速度、進給量和切削深度等。這些參數的選擇直接影響加工效率、表面質量和刀具壽命。一般來說,較硬的材料切削速度相對較低,進給量也較小;而對于較軟的材料,可以適當提高切削速度和進給量。
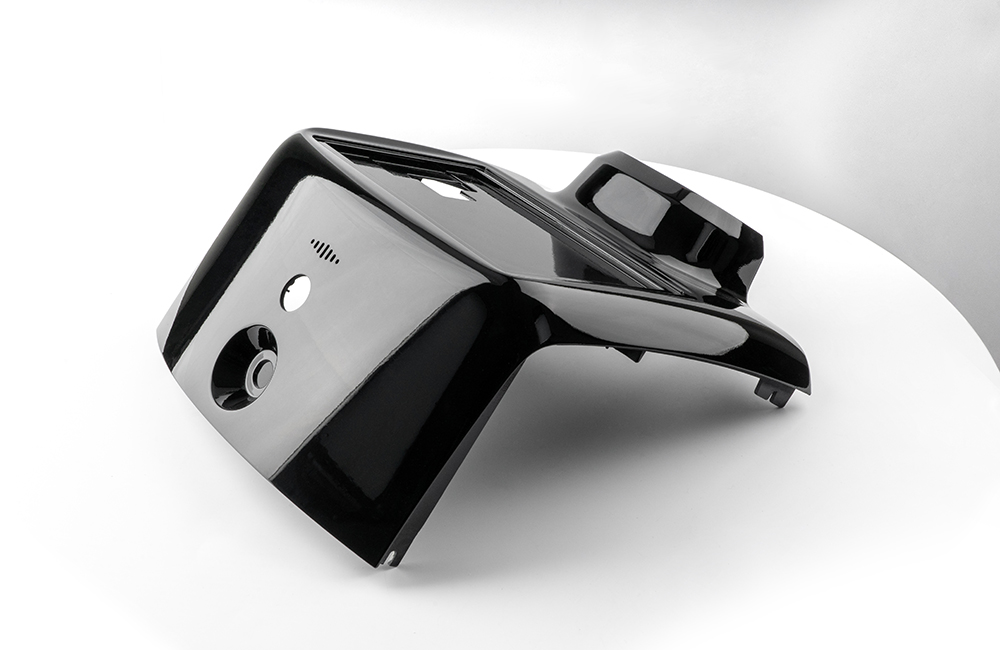
二、CNC編程
生成刀路軌跡:使用CAM軟件,如Mastercam、Cimatron等,將設計好的三維模型轉化為CNC機床能夠識別的刀路軌跡。在編程過程中,需設置合適的加工坐標系、安全平面、退刀方式等參數,并根據零件的形狀和結構特點,選擇合適的加工策略,如粗加工、半精加工和精加工等。粗加工通常采用較大的切削量,快速去除大部分余量;半精加工進一步優化零件的形狀和尺寸精度;精加工則保證零件的表面質量和最終尺寸精度。
模擬驗證:在將程序傳輸到CNC機床之前,務必進行模擬驗證。通過CAM軟件的模擬功能,檢查刀路軌跡是否正確,是否存在刀具干涉、碰撞等問題。模擬過程中可以直觀地觀察到刀具的運動軌跡和加工過程,及時發現并修改潛在的錯誤,避免在實際加工中造成零件損壞和機床故障。
三、裝夾與對刀
零件裝夾:根據零件的形狀和尺寸,選擇合適的裝夾方式。常見的裝夾方法有平口鉗裝夾、卡盤裝夾、專用夾具裝夾等。對于形狀規則的零件,可采用平口鉗或卡盤進行裝夾;對于復雜的異形零件,則需要設計制造專用夾具,以確保零件在加工過程中的定位精度和穩定性。在裝夾時,要注意調整零件的位置,使其與機床坐標系保持一致,并保證裝夾力度適中,避免因裝夾過緊而導致零件變形。
對刀操作:對刀是CNC加工中非常關鍵的一步,其目的是確定刀具與工件之間的相對位置關系。常用的對刀方法有試切對刀法、光學對刀儀對刀法和刀具預調儀對刀法等。試切對刀法是在零件上切削一段小平面或圓柱面,然后通過測量尺寸來計算刀具的補償值;光學對刀儀對刀法利用光學原理,通過測量刀具的反射光來確定刀具的位置;刀具預調儀對刀法則是在刀具裝入機床之前,在預調儀上預先調整好刀具的長度和半徑等參數。無論采用哪種對刀方法,都需確保對刀的精度,以保證加工的準確性。
四、加工過程
粗加工:按照預設的刀路軌跡,啟動CNC機床進行粗加工。在粗加工階段,主要目的是快速去除大量的毛坯材料,使零件接近最終的形狀和尺寸。由于粗加工時切削量大,會產生較多的熱量和切屑,因此需要注意冷卻和排屑問題??墒褂们邢饕哼M行冷卻和潤滑,同時合理設置機床的排屑裝置,確保切屑能夠及時排出,避免影響加工質量和刀具壽命。
半精加工:粗加工完成后,進行半精加工。半精加工的主要作用是進一步優化零件的形狀和尺寸精度,為精加工做好準備。在半精加工時,切削參數相對較小,加工余量也較少,以減小零件的變形和表面粗糙度。
精加工:精加工是保證零件表面質量和最終尺寸精度的關鍵步驟。在精加工階段,使用較小的切削參數,切削深度通常只有零點幾毫米甚至更小,以獲得良好的表面質量。對于一些要求較高的表面,如汽車外殼的外觀面,可能需要進行多次精加工,以達到鏡面效果或滿足特定的表面粗糙度要求。
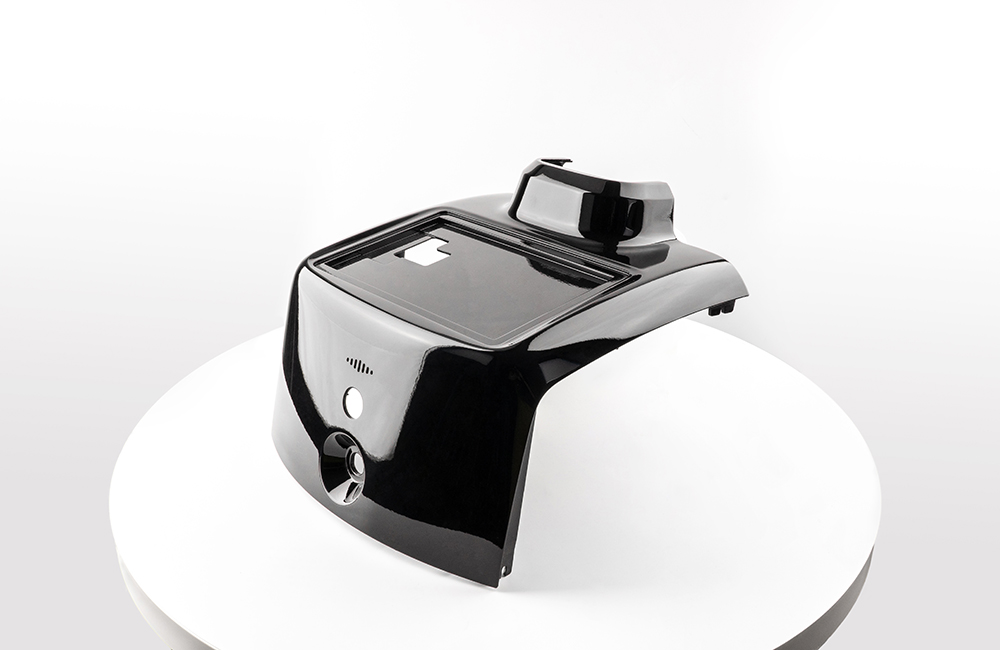
五、質量檢測
尺寸精度檢測:使用三坐標測量儀、卡尺、千分尺等測量工具,對加工后的零件進行尺寸精度檢測。測量內容包括零件的長、寬、高、孔徑、軸徑等尺寸,以及各尺寸之間的位置精度,如平行度、垂直度、同軸度等。確保零件的尺寸精度符合設計要求,一般尺寸公差需控制在±0.01mm至±0.1mm之間,具體公差要求根據零件的重要性和使用要求而定。
表面質量檢測:檢查零件的表面粗糙度、劃痕、氣孔等缺陷。表面粗糙度可通過粗糙度儀進行測量,一般要求Ra值在0.8μm至3.2μm之間。對于外觀面,還需檢查是否有劃傷、凹坑等影響外觀質量的缺陷。此外,還需檢查零件的表面硬度、熱處理情況等,確保其滿足使用要求。
裝配檢測:將加工好的汽車零件外殼與其他相關零件進行裝配檢測,檢查零件之間的配合間隙、裝配精度等。確保零件能夠順利裝配,并且在使用過程中不會出現松動、干涉等問題。裝配檢測不僅可以發現零件本身的問題,還可以檢驗整個加工過程的精度和質量。
六、后處理
清洗:加工完成后,使用清洗劑對零件進行清洗,去除表面的油污、切屑和其他雜質。清洗方式可以是浸泡清洗、噴淋清洗或超聲波清洗等。超聲波清洗能夠有效去除零件表面的微小顆粒和油污,提高零件的清潔度。
去毛刺:檢查零件的邊緣和角落,去除加工過程中產生的毛刺。去毛刺的方法有手工去毛刺、機械去毛刺和化學去毛刺等。手工去毛刺適用于少量和小尺寸的毛刺,使用銼刀、砂紙等工具進行打磨;機械去毛刺則通過專用的設備和工具,如去毛刺機、砂輪機等,對零件進行自動化去毛刺;化學去毛刺是利用化學藥劑與毛刺發生化學反應,使其溶解或脫落,但需注意化學藥劑的選擇和使用安全。
熱處理與表面處理:根據零件的材料和使用要求,可能需要進行熱處理和表面處理。熱處理可以改善零件的材料性能,如提高硬度、強度和耐磨性等;表面處理則可以增強零件的耐腐蝕性、美觀度和耐磨性,常見的表面處理方法有陽極氧化、電鍍、噴漆等。例如,鋁合金零件可以通過陽極氧化處理,在其表面形成一層堅硬的氧化膜,提高零件的耐腐蝕性和耐磨性,同時還可以增加零件的表面光澤度和美觀度。