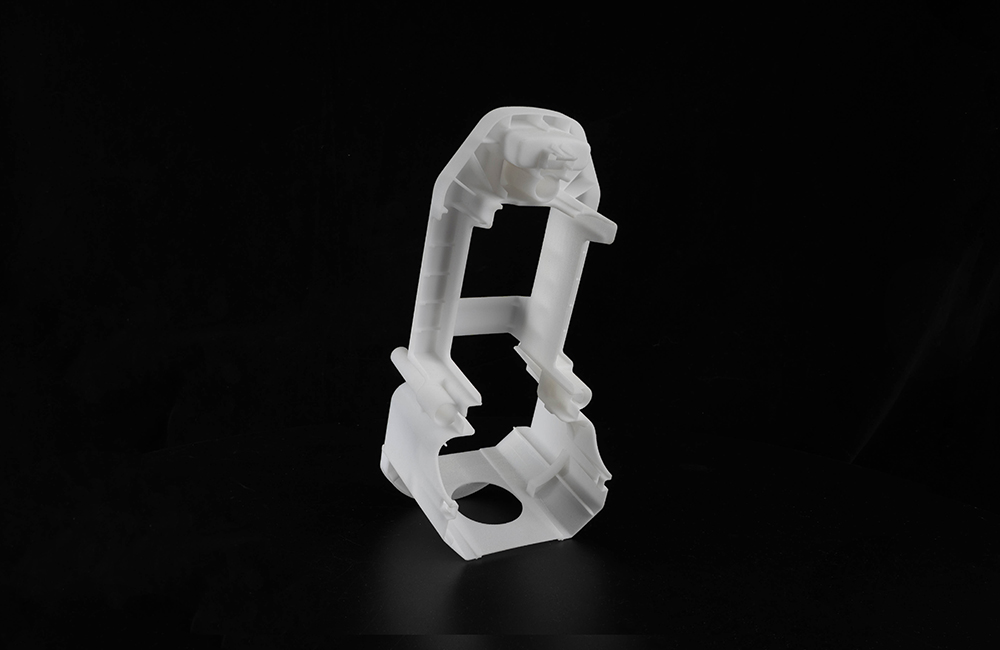
行業/分類:其他手板模型加工
加工方式: 3D打印 使用材料: 樹脂
最小精度: 0.1mm 生產周期: 2~7天
產品尺寸: 15cm*5cm*3cm
后處理: 打磨
SLS(選擇性激光燒結)是一種常用的增材制造技術,在打印汽車零件手板模型方面有以下特點和應用:
技術原理
SLS 技術使用高能量激光束掃描粉末材料床,如尼龍、聚苯乙烯等高分子粉末,或者金屬粉末。激光束根據三維模型的切片數據,有選擇地將粉末顆粒加熱至熔點或燒結溫度,使粉末顆粒相互粘結,形成一層固體截面。然后,工作臺下降一個層厚的距離,重復上述過程,層層疊加,最終構建出三維的汽車零件手板模型。

優點
材料選擇廣泛:可以使用多種材料進行打印,包括尼龍、金屬等,能滿足不同汽車零件對手板模型材料性能的要求,如強度、韌性、耐高溫性等。
高精度:能夠實現較高的尺寸精度和表面質量,一般精度可達 ±0.1mm – ±0.2mm,可滿足汽車零件手板模型對細節和尺寸準確性的嚴格要求。
復雜結構制造能力強:對于具有復雜內部結構、鏤空設計或自由曲面的汽車零件,SLS 打印無需額外的支撐結構,能夠直接制造出復雜形狀的手板模型,有助于縮短產品研發周期和降低成本。
快速成型:從數字模型到實體手板模型的轉化速度快,能夠在較短時間內為汽車研發團隊提供模型,便于進行設計驗證、裝配測試和性能評估等工作,加快產品開發進程。

缺點
設備成本高:SLS 打印機價格昂貴,通常在幾十萬元到數百萬元不等,且維護成本也較高,這增加了汽車零件手板模型的制作成本。
材料成本較高:一些高性能的粉末材料價格相對較高,如某些金屬粉末,導致手板模型的制作成本上升。
后處理復雜:打印完成后,手板模型需要進行后處理,如去除未燒結的粉末、表面打磨、拋光等。對于金屬零件,還可能需要進行熱處理、浸滲等后處理工藝,以提高零件的性能和質量,這增加了制作周期和工作量。

應用場景
外觀驗證:用于制作汽車外觀件的手板模型,如車身外殼、保險杠、格柵等,幫助設計師直觀地評估產品的外觀設計效果,進行色彩、紋理和表面處理的測試,及時發現和修改設計缺陷。
裝配驗證:打印汽車內部結構件和零部件的手板模型,如發動機缸體、變速器殼體、儀表盤支架等,用于裝配測試,檢查零件之間的配合精度和干涉情況,優化產品的結構設計,提高裝配效率和質量。
功能測試:可以制作具有一定力學性能和功能的汽車零件手板模型,如懸掛系統部件、轉向系統零件等,進行初步的功能測試和性能評估,為后續的產品優化和工程設計提供參考依據。