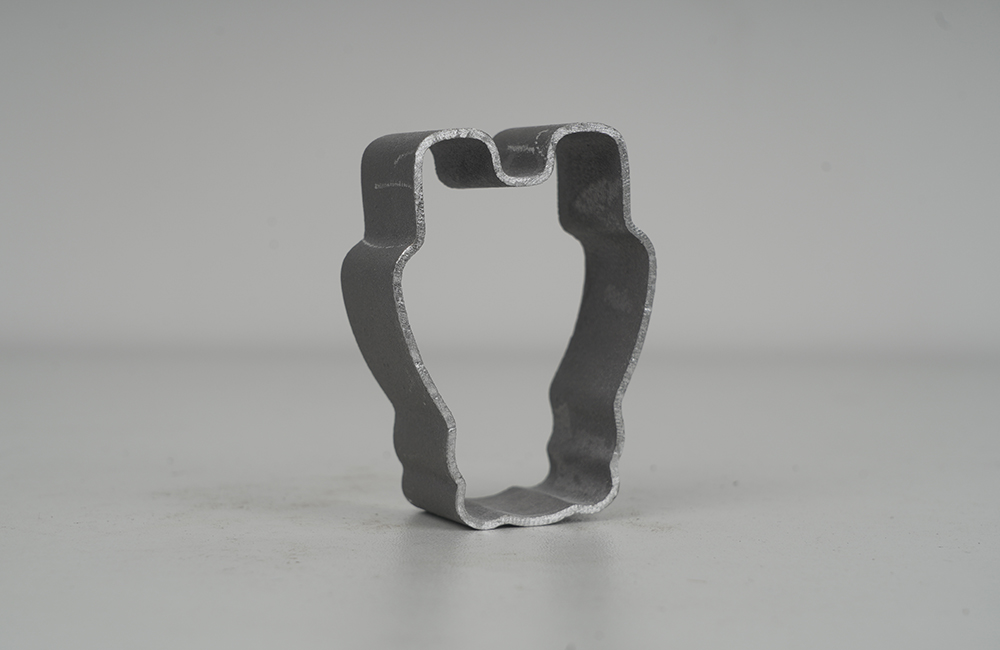
行業/分類:其他手板模型加工
加工方式: 3D打印 使用材料: 金屬
最小精度: 0.1mm 生產周期: 2~7天
產品尺寸: 3cm*2cm*5cm
后處理: 打磨
概述
3D打印汽車金屬零件手板模型是一種利用3D打印技術直接制造汽車金屬零件原型的方法。它可以快速、精確地將數字模型轉化為實體模型,為汽車設計、研發和生產提供了一種高效、低成本的解決方案。與傳統制造方法相比,3D打印無需復雜的模具制造和機械加工過程,能夠大大縮短產品的研發周期和降低成本。
常用材料
- 鋁合金:具有密度小、強度高、耐腐蝕等優點,常用于制造汽車發動機缸體、變速器殼體、底盤零件等。
- 鈦合金:具有高強度、高硬度、耐高溫、耐腐蝕等優異性能,常用于制造汽車發動機氣門、連桿、渦輪增壓器葉輪等高性能零件。
- 不銹鋼:具有良好的耐腐蝕性和機械性能,常用于制造汽車排氣管、制動系統零件、車身結構件等。
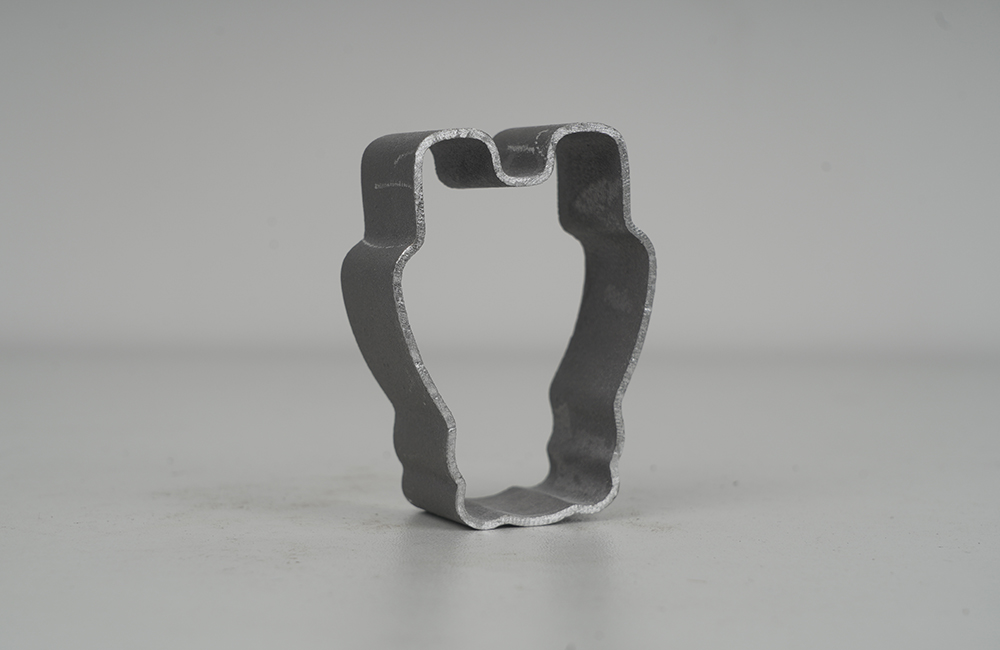
打印工藝
- 選區激光熔化(SLM):利用高能量密度的激光束,按照預先設計的零件模型,逐點、逐層地熔化金屬粉末,使其凝固成型。該工藝可以實現高精度、高復雜度的金屬零件制造,零件的致密度高、機械性能好。
- 激光近凈成形(LENS):通過將金屬粉末輸送到激光束聚焦區域,使金屬粉末在激光的作用下熔化并沉積在基底上,逐步堆積形成零件。該工藝可以實現較大尺寸零件的制造,且具有較高的沉積速率。
- 電子束熔化(EBM):利用電子束作為熱源,在高真空環境下熔化金屬粉末,使其凝固成型。該工藝可以實現快速熔化和凝固,零件的內部組織均勻、性能穩定。
優勢
- 快速成型:能夠快速將設計模型轉化為實體模型,大大縮短了汽車金屬零件的研發周期,加快了產品的上市速度。
- 高度定制化:可以根據客戶的需求,快速制造出各種復雜形狀和結構的汽車金屬零件手板模型,滿足不同車型和客戶的個性化需求。
- 成本效益:在小批量生產和定制化生產中,3D打印技術無需制造模具,降低了生產成本。
- 優化設計:允許設計師在設計階段快速制作原型,進行裝配測試、功能驗證等,及時發現和解決設計問題,優化設計方案。
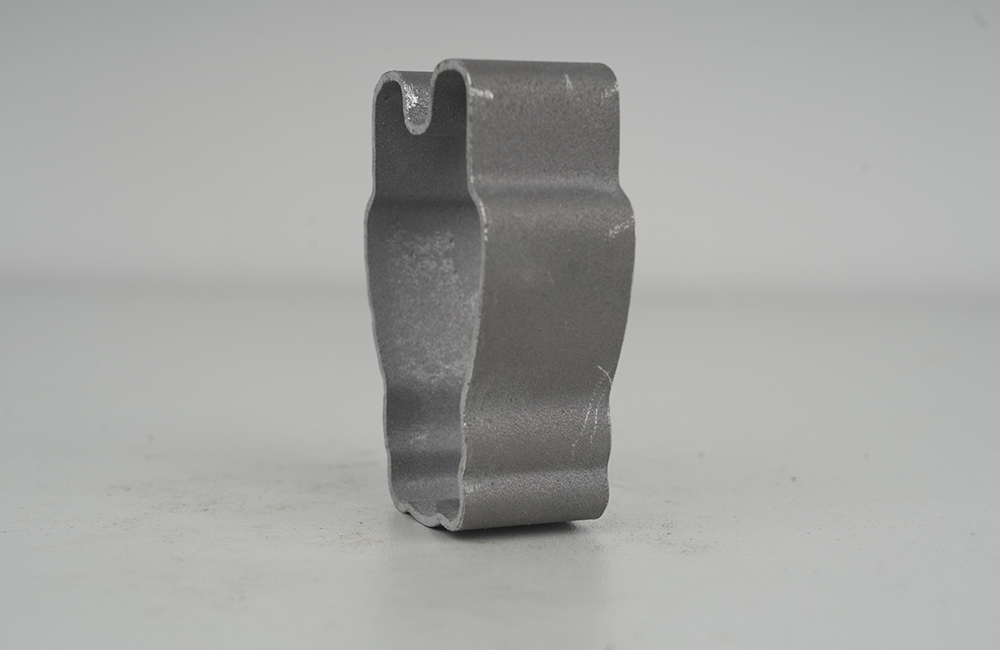
應用場景
- 汽車設計驗證:在汽車設計階段,3D打印金屬零件手板模型可以用于驗證設計的可行性和合理性,幫助設計師及時發現和修改設計缺陷。
- 功能測試:可以制造出具有實際功能的汽車金屬零件手板模型,用于進行各種性能測試,如強度測試、疲勞測試、流體力學測試等。
- 小批量生產:對于一些小批量、高附加值的汽車金屬零件,3D打印技術可以直接進行生產,滿足市場的個性化需求。
- 售后維修:在汽車售后維修領域,3D打印技術可以快速制造出各種汽車金屬零件的替代品,提高維修效率,降低維修成本。
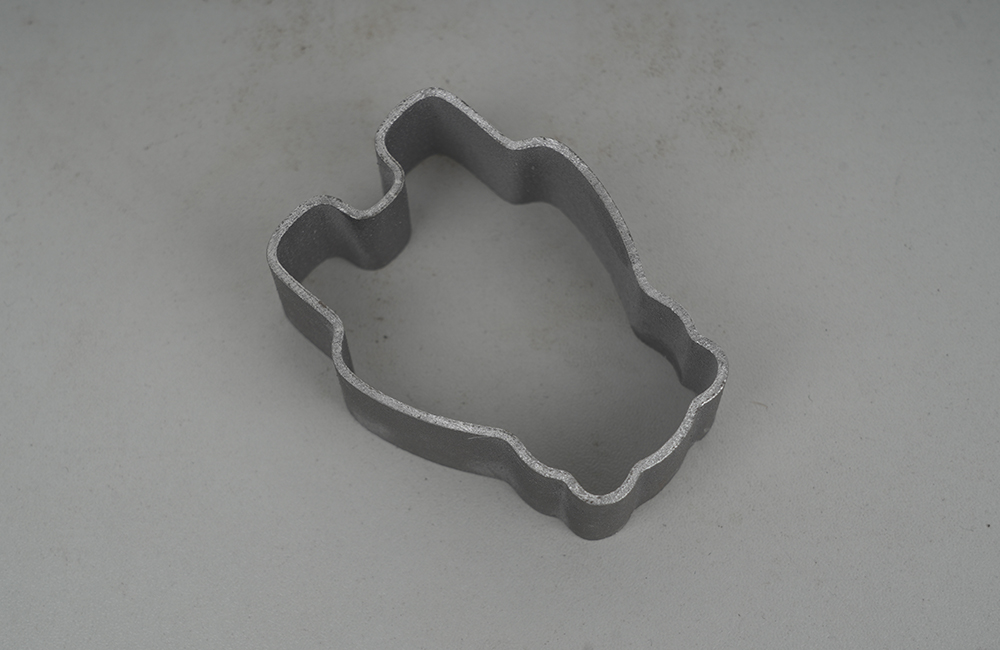
挑戰
- 材料性能:目前 3D打印金屬材料的性能與傳統鍛造、鑄造等工藝相比,仍存在一定差距,如強度、韌性、疲勞性能等。
- 表面質量:3D打印零件的表面質量通常較差,需要進行后續的打磨、拋光等處理,增加了生產成本和生產周期。
- 生產效率:3D打印技術的生產效率相對較低,難以滿足大規模工業化生產的需求。